Design, Optimization, and Verification of Pneumatically Actuated Shape-Morphing Lattices
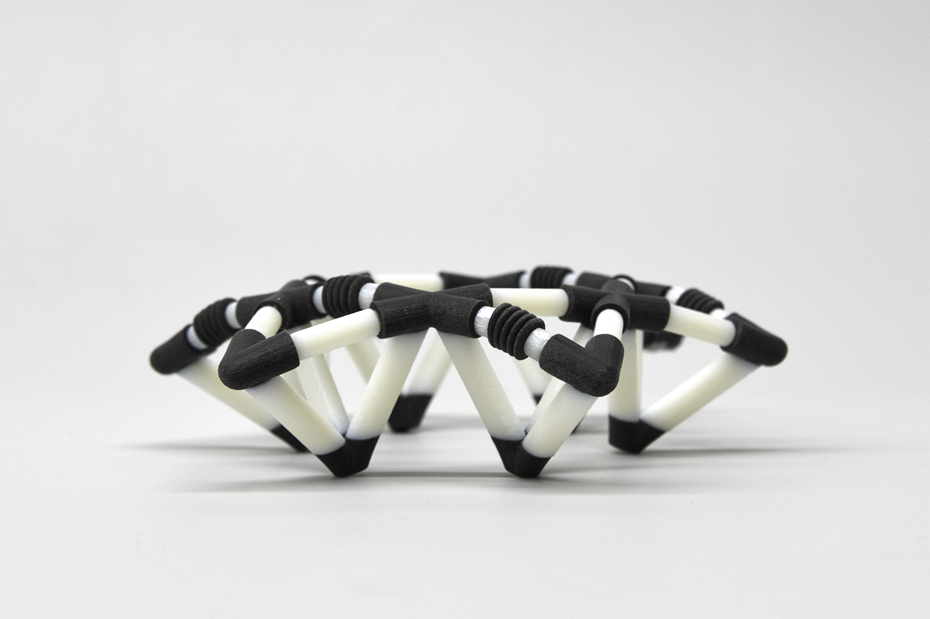
Lattice structures are ubiquitous in nature. Found in crystals to sponges, they have the distinct advantage of being lightweight and porous while retaining robust load carrying capacities. The goal of this research is to go a step further and combine lattices with the fields of soft robotics and 4D printing to design active and adaptive structures.
Soft robotics, contrarily to classical robotics, uses compliant materials to create adaptive robotic systems. The robot controls are directly embedded into its members, whose design is carefully calibrated to generate the desired deformations once pressurized. 4D printing allows the additive manufacturing of objects that undergo shape change upon actuation.
This research combines linear actuator designs from soft robotics with the fabrication advantages of 4D printing to create pneumatic active lattice structures. Macroscopic shape change can be programmed into a structure by replacing static members in the lattice by linear actuators. A computational tool optimizes the necessary positioning of the actuators to best replicate the desired shape change in the deformed lattice. Then, the structure is produced using additive manufacturing and soft robotics’ inspired actuators are placed within it to achieve certain target deformations.
Applications of this research can be found in the automotive industry, in biomedical research, and consumer goods.